News Story
UMD Research Aids Military's Transition to Lead-Free Electronics
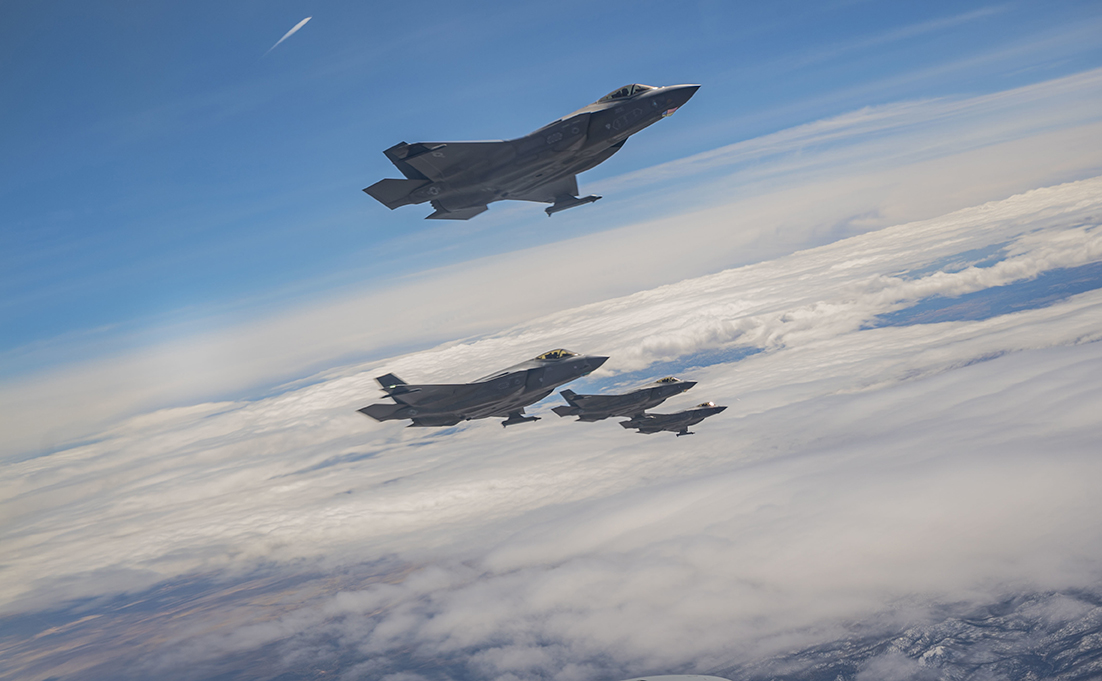
With consumer, computer, and automotive electronics having switched from tin lead solder to lead-free alternatives, the U.S. military is taking similar steps—and drawing on University of Maryland expertise to assist with the transition.
Mechanical engineering research scientist Michael Osterman, who directs consortia and lab activities at the Center for Life Cycle Engineering (CALCE), is co-leading a multi-university project that aims to help the DoD assess different types of unleaded solder and determine which ones are best for a given system. CALCE has been supporting the electronics industry for over 30 years by conducting consortium and contract funded research as well as fee-for-service projects for organizations.
Osterman is co-leading a team that also includes experts from Auburn University and Purdue University, all with decades of experience in the study of lead-free alternatives such as SAC305—a widely used solder containing tin, silver and copper. The Solder Performance and Reliability Assurance Project seeks to provide the framework for characterizing solder and assessing the performance of solder in defense applications.
“We’re developing tools that will enable the military to make sound decisions about what kinds of solder to use,” Osterman said. “They’ll be able to determine whether a particular lead-free solder will create reliable electronics in specific applications; they’ll be able to compare the solder to other lead-free varieties and also to the performance of tin lead solder.”
Health concerns, regulations drive transition
Solder is a critical ingredient in any electronics system, used to create stable electrical interconnections and ensure current flows only where it is supposed to do so. As an interconnect, solder is subjected to cyclic loads that can cause the solder to degrade and fail. The ability of determine the life of solder interconnects in applications is critical to ensuring reliable electronics. For decades, electronics depended on lead-based solder and developed electronics with an understanding of how lead-based solder performs. Health risks associated with the toxicity of lead, however, have spurred the consumer electronics industry to adopt non-lead alternatives.
Aerospace and defense companies have continued to utilize tin-lead solder, largely because they lack experience with lead-free solder and are familiar with the properties of tin-lead solder. But the continued reliance on tin-lead solder is fast becoming untenable. A 2004 move by the European Union (EU) to ban leaded solder from consumer electronics prompted manufacturers to redesign their products, often in ways that can’t easily be retrofitted to work with lead.
“The transition is a must, but the military needs a framework that will allow it to maintain high levels of reliability and performance,
Dr. Michael Osterman, Center for Advanced Life Cycle Engineering (CALCE)
More recent regulations by the EU have prompted automakers to follow suit. Since defense companies obtain their electronic parts from the same manufacturers that serve the consumer market, the DoD has to spend tens of millions of dollars each year to re-engineer them so that they’ll work with the tin-lead solder assembly process.
“The transition is a must, but the military needs a framework that will allow it to maintain high levels of reliability and performance,” Osterman said. “Decision makers need to know what information is essential and where they can obtain that information.”
Examining specific applications
Part of the project, he said, involves examining a broad range of defense applications—from planes to weapons systems—to gauge the conditions in which a solder is being used, and then assess how well that solder will perform in that context.
Among other concerns, Osterman and his collaborators will be addressing the phenomenon known as “tin whiskers,” in which a connection can sprout conductive, needle-like structures that can lead to short circuits.
“Adding lead to tin is a known tin whisker mitigation strategy, but lead-free electronics removes this approach. We will be working to quantify the tin whisker risk with the lens of 15 years of lead-free electronics and effective tin whisker mitigations methods,” Osterman said.
Osterman and his colleagues at Auburn and Purdue are conducting their research under the auspices of the Defense Electronics Consortium (DEC), established by the U.S. Partnership for Assured Electronics (USPAE) with the broad aim of mitigating defense risks created by the contraction of the U.S. electronics manufacturing sector over the last 20 years.
Congress has allocated $15 million to the DEC for the first two years with an additional $25 million expected in 2022 to cover the planned 5 – 7-year project. The first year funding of $3.9 million to DEC is being distributed to the three universities for the first year, including $830,000 for UMD.
Published April 22, 2021